Robotic welding offers greater precision and consistency compared to manual welding. When considering how accurate is robotic welding, it means performing tasks with exactness, repeating the same process consistently, and maintaining tight tolerances. While skilled manual welders can achieve high accuracy, robotic welding remains consistently precise over time. Robots can repeat their work within ±0.02 mm to ±0.1 mm, significantly enhancing quality and safety. Automated welding reduces errors caused by fatigue and ensures uniform quality. Many industries rely on robotic welding for high precision and reliable results. For advanced robotic welding solutions, EVST provides trusted expertise.
Key Takeaways
- Robotic welding is much more accurate than manual welding. It keeps welds very close to the right size, like ±0.1 mm. Automation helps stop mistakes people make when they get tired or lose focus. This means the welds are more steady and there are fewer errors. Robotic welding also makes things faster to build. It saves money over time. It helps make welds safer and more dependable for many industries.
Welding Accuracy
Accuracy Meaning
Welding accuracy means making welds that fit exact sizes each time. Both robotic welding and manual welding depend on three things. These are precision, repeatability, and tolerances. Precision is how close a weld is to the right size or shape. Repeatability means making the same weld again and again with little change. Tolerances are the small differences allowed from the perfect size, like ±0.1 mm for robotic welding. Good results in these areas make welds better. Robotic welding is special because it keeps being precise and steady for many hours. Automated welding uses sensors and controls to keep welds inside tight tolerances. This helps stop mistakes and keeps people safe.
Measuring Accuracy
Special tools and strict rules are used to check welding accuracy. Groups like the American Welding Society (AWS), ASME, and ISO make these rules. Standards like AWS D1.1 and ASME Section IX help make sure welds are strong and safe.
Welders use different gauges to check weld size, seam evenness, and alignment. Some common tools are:
- Fillet welding gauges for checking throat thickness and leg length
- Welding seam gauges for checking seam height and evenness
- Digital gauges for very exact jobs in places like aerospace
Micrometers and rulers also help measure length, width, and thickness. Digital tools can be even more exact and steady. Tolerances help pick which tool to use. The 10:1 rule says tools should be ten times more exact than the weld’s tolerance. By using these steps, both robotic welding and manual welding can meet high standards. But robotic welding gives more steady results and better control.
How Accurate Is Robotic Welding vs Manual Welding
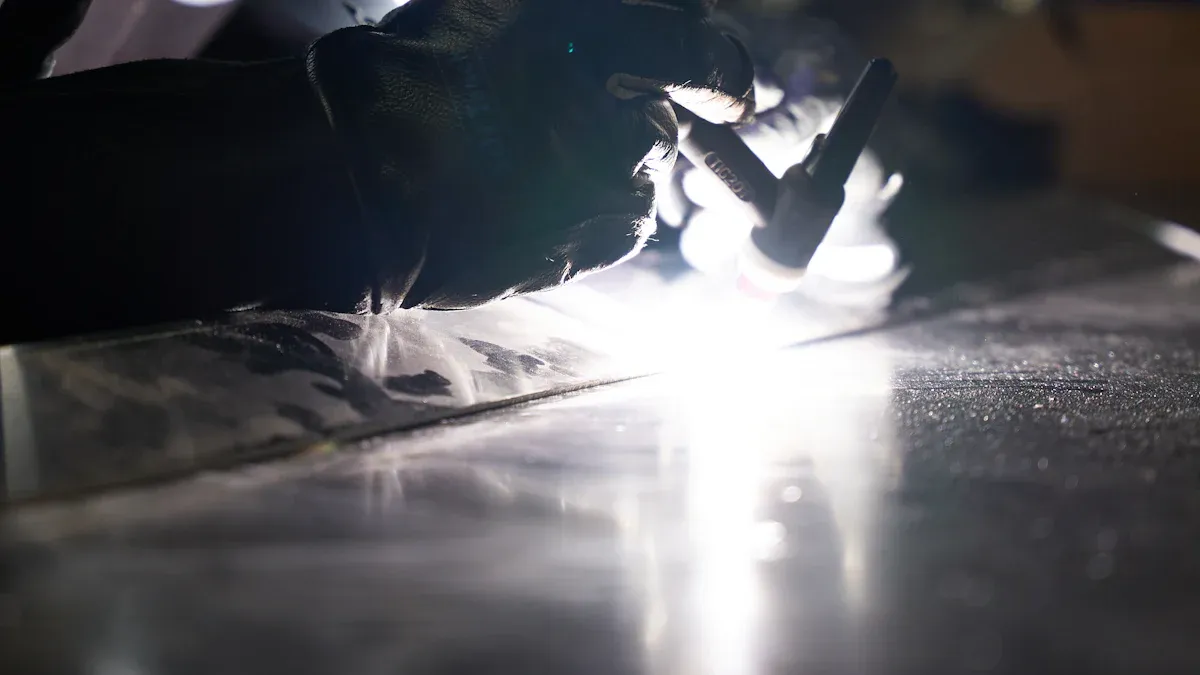
Consistency and Repeatability
Consistency means making welds the same way each time. Repeatability is doing this again and again without changes. Manual welding depends on how skilled and focused the welder is. Some welders make great welds, but even the best can have small differences. Getting tired or distracted can cause these changes.
Robotic welding uses machines that follow set instructions. Robots move the same way, at the same speed, and angle every time. They do not get tired or lose focus. This makes their welds more accurate and steady. For example, automatic orbital welding uses a spinning electrode and checks the weld as it happens. Special turntables and positioners help robots repeat moves, which is important for car and airplane factories.
Gage Repeatability and Reproducibility (Gage R&R) checks if measurements are reliable. It looks at how much results change when different people measure the same weld. A good system has less than 10% change, which helps keep welds good.
The table below shows how manual and robotic welding compare for accuracy and consistency:
Criteria | Manual Welding | Robotic Welding |
---|---|---|
Quality & Consistency | Depends on the worker; can change | Almost always the same; steady welds |
Positional Accuracy | ±1–2 mm | ±0.1 mm |
Robotic welding also uses sensors and computers to watch for problems. They can fix mistakes right away. This keeps welds steady and lowers errors.
Human Error vs Automation
Manual welding depends on the person doing the job. Even good welders can make mistakes. Getting tired, shaky hands, or losing focus can cause errors. Weld quality can change from one shift to another or even in one day. Learning to weld well takes a long time.
Automated welding removes many of these problems. Robots do not get tired or lose focus. They follow instructions exactly, so there are fewer mistakes and more steady welds. Some robots use sensors and artificial intelligence to check welds as they go. If something is wrong, the robot can fix it right away.
The table below shows some differences between manual and robotic welding:
Aspect | Manual Welding | Robotic Welding |
---|---|---|
Weld Quality Variation | ±1–2 mm because of tiredness or skill | ±0.1–0.3 mm, stays the same all day |
Precision Factor | 5–10 times less exact than robots | Very steady, almost perfect welds |
Error Sources | Tiredness, changes in skill, mistakes | Gets rid of human mistakes |
Training Time | 6–18 months to learn; 2–3 years to be expert | Only hours or days, fewer mistakes |
Robotic welding uses live data and smart controls to keep welds inside set limits. This makes welds safer and more reliable. It also helps make lots of parts with few mistakes.
Tolerance Levels
Tolerances are the allowed differences from the perfect weld. Manual welding usually has bigger tolerances because people cannot always make the same weld. Good welders can adjust for changes, but small mistakes can still happen.
Robotic welding can keep tighter tolerances. For spot welding, robots can stay within about ±1 mm. For arc welding, they can be even closer, around ±0.5 mm. Robots use set moves and tracking systems to stay inside these limits. This control is important for products that need to be safe and high quality.
Note: Robots can keep tight tolerances, but people can sometimes fix surprises in the workpiece. For big parts, robots may need extra tools to track joints and stay accurate.
How accurate is robotic welding? Robots can keep welds within ±0.1 mm sometimes, which is much better than the ±1–2 mm for manual welding. This higher accuracy means better welds and less waste. Automated welding helps companies meet strict rules and make steady products.
Practical Impact of Welding Robots
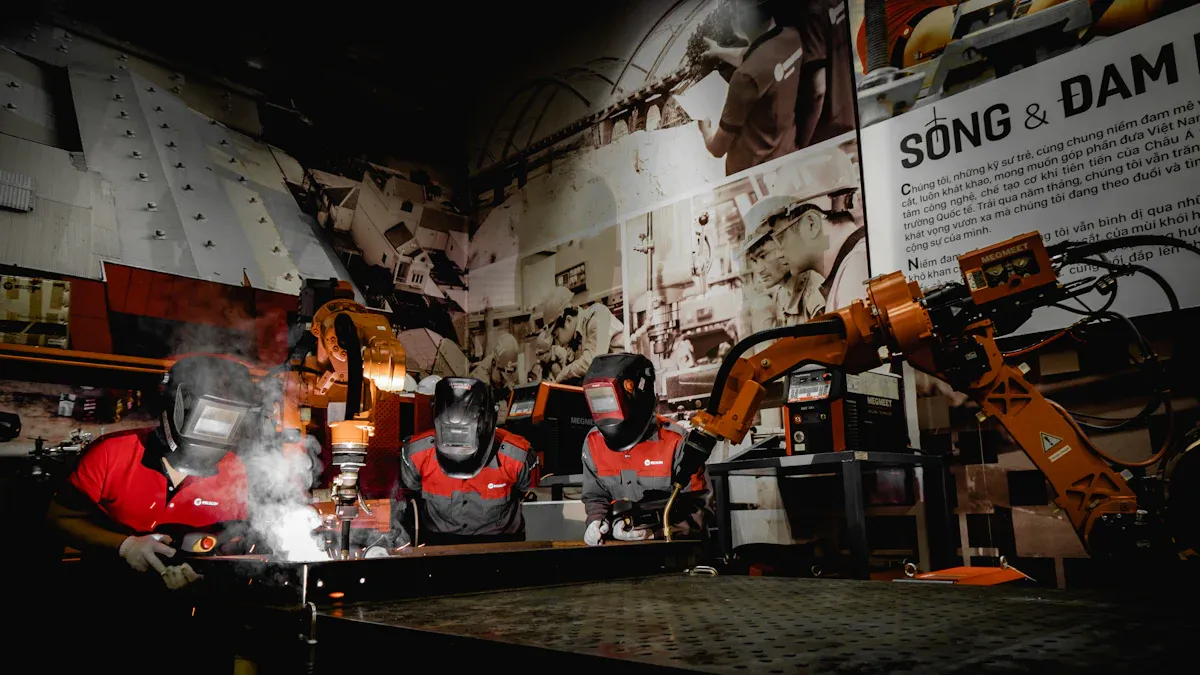
Quality and Defects
Robotic welding makes welds that are very good. Robots move in exact ways and use smart sensors. This helps stop waste and fixes before they happen. Robots do not over-weld or make too much spatter. Sensors and cameras find problems early, so fewer bad welds are made. For example, one shop used a collaborative robot. They went from making 1 part to 6 parts in 20 minutes. This shows robots help make more parts and better welds.
A new study looked at different ways to find weld problems. The best model found welds right 97.35% of the time. It tracked welds with a 96.65% fitting degree. The error for weld depth was only -0.06 mm. These numbers show robots make welds that are very steady and high quality.
Metric | Proposed Model | MOSSE | DSST | YOLOv4 | Faster-RCNN |
---|---|---|---|---|---|
Tracking Fitting Degree (%) | 96.65 | 80.35 | 86.67 | N/A | N/A |
Weld Detection Accuracy (%) | 97.35 | N/A | N/A | 90.65 | 83.21 |
Weld Penetration Depth Error (mm) | -0.06 | N/A | N/A | 0.11 | 0.13 |
Production and Cost
Robotic welding helps make things faster and saves time. Companies say they make more products and spend less money. Ford Motor Company made 40% more products after using robots. JCB made work 30% faster and had 18% less rework. Valtra saved 25% on costs and delivered 20% faster.
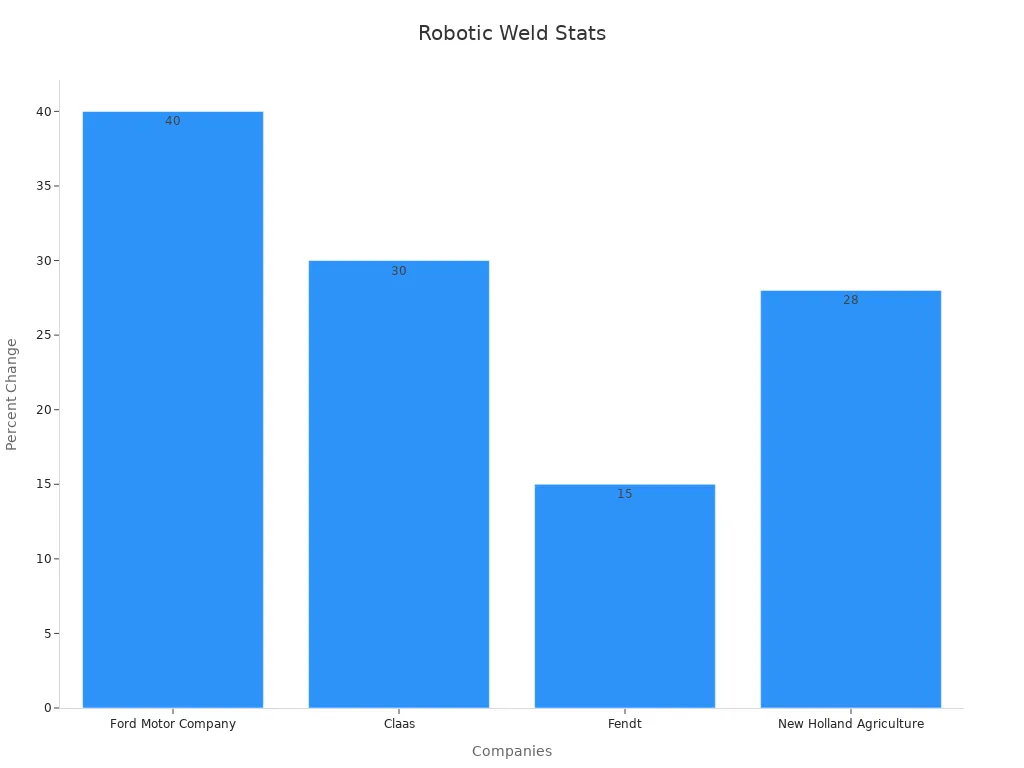
Most robotic welding systems pay for themselves in one to three years. Companies save money because there is less waste and fewer mistakes. They also need fewer workers. After paying for the robots, companies keep saving money. This makes robotic welding a good choice for businesses that want better quality and more products.
Application Scenarios
Many companies use robotic welding to fix real problems. Hutchison Inc. made better welds and met more orders when workers were hard to find. Latham Pools saved money and used fewer workers. Advanced Drainage Systems made pipe welding safer by using robots. Hipshot Products got rid of hand polishing and made better welds.
Robotic welding also helps companies like Will-Burt Co. and Seibel Modern. They do less touch-up work and can track what they make. Pitts & Spitts made more products, and Diamond Doors brought work back to their own shop.
Robotic welding can do hard jobs with special features. Offline programming and adaptive welding help with tricky work. EVST gives solutions that help many industries get great welds every time.